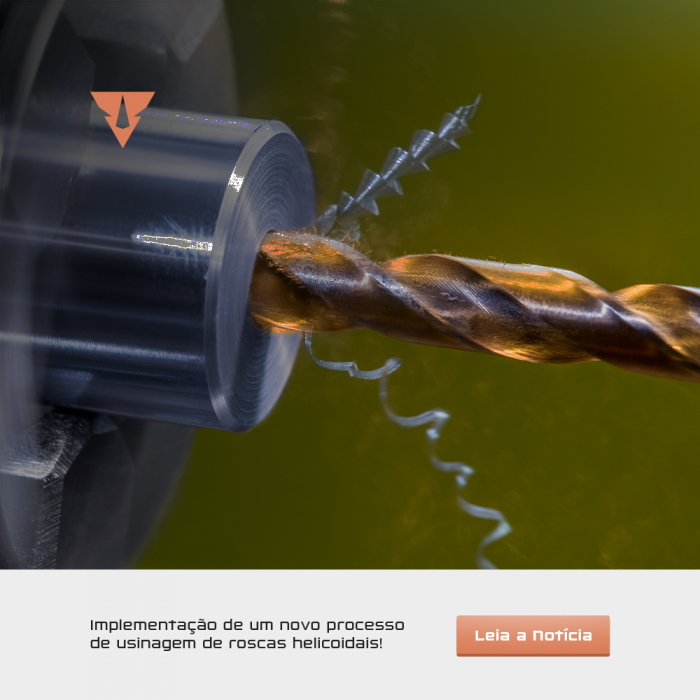
A disputa do mercado está cada vez mais acirrada. O crescimento da concorrência faz com que os processos produtivos das empresas se transformem para se adaptar a um novo ambiente.
Tendo como um dos principais objetivos a redução de custo de produção dentro de uma empresa, deve-se observar a importância das ferramentas de corte na prática de uma manufatura mais eficiente, especificamente nos processos de usinagem, apresentando grande representatividade da indústria mundial.
A otimização dos parâmetros de corte das ferramentas, já vem sendo realizada há muito tempo, baseada principalmente na redução do tempo de fabricação, que é alcançado com a utilização da ferramenta correta, utilização de avanços e profundidades de corte que vão de acordo com a capacidade da máquina.
A tecnologia proporciona a criação de máquinas e ferramentas mais eficientes, apresentando novos recursos de usinagem que possibilitam às indústrias a confecção de produtos mais complexos, com alta qualidade e custos menores de produção.
É necessário estar atento aos recursos que surgem, já que a informática sempre possibilita avanços progressivos para a indústria de manufatura.
Neste artigo, vamos compreender a criação de elementos de máquinas, usinagem, tecnologias, gestão empresarial e outros assuntos que integram o desenvolvimento de projetos.
Elementos de máquinas
Conforme Norton, o parafuso sem fim é constituído por uma rosca helicoidal. Ele se acopla com uma engrenagem sem-fim, também chamada de coroa ou roda sem-fim. Tem capacidade de produzir razões de engrenamento muito grandes. A sua principal desvantagem é o baixo rendimento quando comparado com outros engrenamentos.
Os redutores Coroa/Sem fim possuem um rendimento de trabalho em torno de 85%. O parafuso sem fim pode possuir uma ou mais entradas e a quantidade de entradas está relacionada com o avanço obtido por volta, isto é, para saber o avanço de um parafuso sem fim, basta multiplicar o passo do parafuso, que é a distância entre filetes consecutivos de rosca, pelo número de entradas.
Características da rosca
A rosca helicoidal possui características definidas pela NBR 5876, como uma superfície composta, gerada por um ou mais perfis, quando todos os seus pontos descrevem hélices.
O ângulo do avanço na rosca cilíndrica é o ângulo formado pela hélice da rosca na linha efetiva, com o plano perpendicular ao eixo.
O ângulo de hélice é o complemento do ângulo de avanço. É feito pela hélice da rosca em relação ao eixo.
Para calcular o ângulo de hélice da rosca fator importante nesta usinagem, deve-se usar esta equação, Eq. (1):
Onde:
a: ângulo de hélice
i: avanço (passo x N? de entradas)
n: número de entradas
p: passo
d: diâmetro efetivo
Processo de rosqueamento
É importante destacar as características dos parafusos sem-fim. O processo de rosqueamento trata-se, de uma usinagem destinada para obtenção de filetes, por meio da abertura de um ou vários sulcos helicoidais de passo uniforme, em superfícies cilíndricas ou cônicas de revolução.
Para isso, a peça ou a ferramenta gira e uma delas se descola simultaneamente, segundo uma trajetória retilínea paralela ou inclinada ao eixo de rotação.
Para roscas com uma profundidade maior, como nos casos de parafusos sem-fim de redutores de velocidade, a recomendação é para que sejam feitos cortes sucessivos normalmente ao seu eixo ou avançar em uma direção inclinada, com o avanço composto, que seria um avanço adicional (transversal + longitudinal), ao longo do flanco da rosca.
A ferramenta usada pode ter um ângulo de saída adequado, já que o corte será apenas de um lado, pela ação do gume principal. O gume secundário deve ter uma folga em relação ao segundo flanco de aproximadamente 1°, possibilitando mais condições de usinagem favoráveis.
A posição da ponta da ferramenta deve ser ajustada exatamente no centro da peça. Se a ferramenta colocada for muito alta, fica com muito contato com a superfície de incidência, produzindo aquecimento excessivo e superfície rugosa. Se a ponta estiver muito baixa, modificações nos ângulos normais da ferramenta podem acontecer, sobrecarregando-a excessivamente, correndo o risco de quebra-la.
Utilizado para a execução de roscas, outro método de manufatura é o processo de fresagem. Com ferramenta acionada de perfil único, que permite obter economicamente roscas precisas de diversos tipos, é um processo usado na execução de roscas, em geral, de passo grande.
A peça gira lentamente, produzindo a velocidade do avanço, enquanto o cabeçote porta-fresa desloca-se paralelamente, ao eixo da peça, de um passo para cada volta da peça. O cabeçote porta-fresa deve ser basculado de um ângulo igual ao de avanço da rosca.
O centro de basculamento deve coincidir com a li há de centro da forma a obter. No caso de roscas de passo muito grande ou de várias entradas, o cabeçote porta-fresa deve ter um suporte externo para conferir-lhe maior rigidez.
Características da ferramenta de rosqueamento
A geometria da ferramenta de corte exerce uma grande influência no desempenho do processo de rosqueamento. Por melhor que seja o material da ferramenta, se a sua geometria não estiver preparada de forma adequada, a operação não tem êxito.
Existem diversos materiais que são utilizados para a fabricação de ferramentas de corte. É comum encontrar no mercado ferramentas de aço-rápido, que possuem boa tenacidade, e as de metal-duro, onde o material é obtido por sinterização, apresentando boa estrutura, dureza elevada, boa resistência ao desgaste, a temperaturas elevadas e a compressão.
A geometria da ferramenta denomina-se por diversas características. A cunha cortante, parte da ferramenta na qual origina-se o cavaco, podem ser retilíneas, angulares ou curvilíneas. As superfícies de folga também podem ser citadas. Estas são as superfícies da cunha cortante que confrontam com as superfícies de corte e de saída. É superfície da cunha cortante onde o cavaco se forma.
Ângulos da ferramenta
O ângulo de incidência varia entre cinco e dez graus. Porém, é importante observar que por conta do ângulo de hélice da rosca, o ângulo efetivo de incidência é reduzido num flanco e aumentado em outro.
O ângulo efetivo de incidência deve ter pelo menos entre três e cinco graus. Em roscas de passo muito grande uma das estruturas deve ser maior, resultando em uma ferramenta assimétrica.
O ângulo efetivo de saída também fica diferente nos dois flancos, produzindo condições desfavoráveis de usinagem. Como forma de correção, especialmente no caso de ângulos de hélice maiores do que dez graus, o ideal é que monte-se o cabo da ferramenta inclinado. Neste caso, ocorrem deformações no perfil da rosca que podem ser corrigidos por compensação adequada no perfil da ferramenta.
Acabamento superficial da usinagem
O acabamento superficial, geralmente especificado em projetos mecânicos, como a representação de rugosidade, consiste em um conjunto de irregularidades com espaçamento que tende a formar um padrão ou textura em uma superfície.
Estas irregularidades estão presentes em todas as superfícies reais. Por mais que estas estejam em perfeito estado, muitas vezes constituem uma herança do método de fabricação, empregado na obtenção da superfície.
A importância da rugosidade justifica-se pela relação com outros fatores como a precisão e a tolerância que é extremamente importante em redutores de velocidade. Neste caso, superfícies com rugosidades mais pronunciadas estarão expostas a desgastes mais intensos do que sofreriam se tivessem um melhor acabamento superficial.
A textura superficial pode estar relacionada ao desempenho do componente fabricado no que diz respeito a sua capacidade de operação dentro dos padrões de qualidade. Um bom exemplo é o caso de duas superfícies de contato em movimento relativo como o processo de rosqueamento que apresenta alterações na superfície da peça. Na ordem de grandeza de micrometros que podem reduzir a resistência da fadiga das peças, é necessário um acabamento superficial pós máquina, com retífica. No caso das roscas helicoidais, é ideal aumentar seu rendimento dentro de um redutor e atender normas internacionais de qualidade.
CNC/CAD/CAM
O Comando Numérico Computadorizado é um equipamento eletrônico capaz de receber informações através de uma entrada própria de dados. Em forma de comando para a máquina, estas informações por sua vez são responsáveis pelo acionamento de motores que darão a máquina os movimentos desejados de modo que, sem a intervenção do operador, as operações sejam realizadas na sequência.
As máquinas CNC são programáveis e possuem ciclos de usinagem do fabricante para facilitar a programação manual, principalmente na produção de geometria regulares. O sistema CAD/CAM é definido como um gráfico interativo computacional equipado com software que realiza as tarefas de projeto e manufatura. O sistema CAM faz a leitura das geometrias da peça, armazena em um arquivo gráfico criado no software de CAD e desenvolve a geração de programas CNCs, seguindo os dados fornecidos pelo programador usuário do CAM.
Procedimento metodológico
Para a implantação do processo de rosqueamento CNC, a rosca helicoidal teve necessidade de passar por um procedimento metodológico. Foram feitos testes de usinagem em um torno CNC. O Romi Centur 30D com comando numérico da Siemens foi utilizado.
Uma usinagem de quatro corpos de prova foi feita utilizando um inserto intercambiável de rosqueamento específico. Para a fixação deste inserto, foi projetado um suporte de fixação no software de engenharia CAD. Foi também realizado um programa numérico computadorizado, implementando uma lógica algorítmica, afim promover condições de usinagem mais favoráveis.
Depois de efetuado os procedimentos de manufatura, testes de rugosidade nos corpos de prova foram comparados ao atual processo destas roscas com o processo de usinagem proposto neste artigo.
1. Rosca helicoidal
A rosca helicoidal apresentada neste artigo possui características importantes para efetuar um movimento de transmissão. As características da figura são as seguintes:
Diâmetro externo: 31,26mm
Diâmetro efetivo: 26,64mm
Diâmetro interno: 21,25mm
Ângulo de hélice: 9,84°
Passo: 7,25mm
Entradas: 2
2. Suporte projetado para a fabricação de roscas
Para executar o processo de usinagem da rosca em questão, um software de engenharia CAD foi projetado um suporte específico para esta aplicação.
É necessária a aplicação de uma inclinação no próprio suporte quando se trata de uma rosca com passo considerado grande. É o que acontece com a rosca deste projeto, que deve inclinar-se sob o suporte com o ângulo igual ao da hélice da rosca.
Esta ferramenta apresenta características precisas especialmente na fixação do inserto. Para o seu desenvolvimento foi utilizado o quarto eixo, mantendo em perfeito esquadrejamento do suporte já que foi totalmente usinado sem ser removido da máquina. A programação foi elaborada no software de engenharia CAM e o material usado foi o aço.
Na sequência foram levantados todos os valores para a fabricação desse suporte, a fim de verificar o custo do investimento da implementação deste novo processo.
3. Descrição dos processos atual e composto
Para uma ampla visualização da implementação do processo de rosqueamento CNC se faz necessário a análise entre o processo proposto e o atual, a fim de observar se a intenção deste artigo atinja realmente as exigências de uma manufatura eficiente.
3.1 Processo atual de fresagem de roscas
Antes de usinar a rosca em questão, deve-se aplicar as medidas específicas do eixo sem-fim, empregadas no próprio torno CNC.
Depois de efetuadas as medidas referentes ao sem fim, deve-se inicializar a produção de roscas. Este processo trata-se de um único método de fresagem por ferramenta acionada de perfil único que dura em média, 27 minutos de usinagem.
O processo de fresagem de roscas permite uma fabricação mais econômica e de diversos tipos. Porém, ele apresenta alto índice de rugosidade na usinagem, já que a máquina não apresenta uma estrutura rígida e precisa.
Em decorrência da usinagem ser efetuada em um tempo considerável, a máquina acaba se tornando um gargalo de produção, necessitando efetuar horas extras periodicamente para produzir a demanda de peças.
Também é necessário afiar a ferramenta de corte a cada dez peças usinadas. Feito de forma manual, não apresenta características geométricas, adequadas para a produção de roscas trapezoidais. Esta ferramenta é desenvolvida na própria empresa e tem baixo custo de produção, cerca de R$ 300 por peça. A vantagem está no tempo de vida útil, que é de aproximadamente seis meses.
Como este atual processo de usinagem apresenta desconformidade geométrica, é necessário um acabamento nas roscas, pós máquina, este torna-se um pouco mais demorado pelo alto índice de rugosidade apresentado.
Na produção de fresagem de roscas, é necessário deixar um sobremetal de acabamento para a fixação da peça na máquina. Este trabalho apresenta características de vedação do redutor, não podendo ser comprometido por qualquer desconformidade. A peça deve voltar ao torno CNC afim de aplicar esta medida de precisão, encarecendo ainda mais o processo.
Conclusão
Com a proposta sugerida, bem como a mudança no roteiro de fabricação, houve uma redução de 12,1% nos custos de fabricação de 100 peças por lote. Levando em consideração que se obteve lucro mesmo com o preço da máquina CNC sendo o dobro do preço do processo atual.
Com a produção executada no torno CNC, é fato afirmar que a qualidade e precisão da peça aumentaram consideravelmente. Atrelado ao teste de rugosidade, que obteve resultado satisfatório, permite ao redutor desempenhar um melhor rendimento pois o atrito entre as partes diminui com a implementação do processo proposto.
É fato afirmar que a geometria do inserto, ângulos de saídas de corte bem projetado obtém-se ótimos resultados de usinagem, atrelado também a importância do ângulo de hélice da rosca, que deve ser transmitido para o suporte, evitando esforços de usinagem.
O corpo de prova que melhor atendeu a qualidade superficial foi o número três, apresentando uma redução da rugosidade em 60%. Tendo em vista que o tempo de usinagem foi diminuído quase pela metade do tempo atual, a empresa tem a capacidade de produzir o dobro de peças sem precisar adquirir novos equipamentos.
O aumento do RPM da máquina diminui, consideravelmente, o tempo de usinagem. Observa-se a importância dos parâmetros bem calculados nesta etapa, deixando esta parte do estudo em aberto para possíveis análises, já que dependendo do material do inserto, seu revestimento superficial e análise do mesmo, atrelado também a utilização dos fluídos de corte específico, pode-se melhorar os parâmetros de corte afim de reduzir o tempo de usinagem.
Fonte: Revista Ferramental